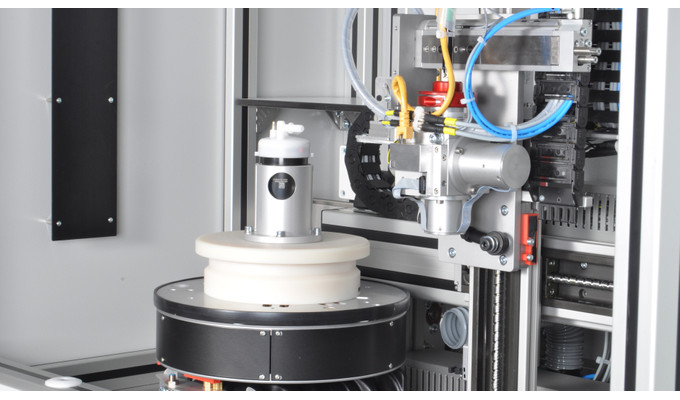
Application
The use of lasers and laser technologies brings a new dimension to industrial production, which corresponds to the ever-increasing demands for increasing its quality and efficiency. Modern laser systems and technologies surpass conventional tools by combining speed, accuracy, performance and flexibility. Ease of operation and ease of maintenance enable immediate and reliable integration into the production process.Lasers are used in the initial and final stages of production, when they are commonly used for marking, engraving, cutting, drilling, welding ... Today, the laser is no longer considered only a state-of-the-art technology, but also a tool that helps to do work faster and better.
Laser marking and engraving
Whenever the question of production marking arises, the use of a laser is an elegant and effective solution. The laser creates a stable, mechanically resistant, highly contrasting and otherwise inimitable marking on the surface of the material with high accuracy. Everything takes place in a single short operation without the use of chemical additives and ink or mechanical interventions in the structure of the material. Practically any metallic or non-metallic material can be marked with a suitable type of laser (fiber, Nd: YAG, Nd: YVO4 or CO2), while the surface of the marked product can have a variable shape and different surface finish. By changing the parameters of the laser, it is possible to continuously go from the surface marking in a few microns layer of material to laser engraving to a greater depth.
Laser cutting and drilling
Industrial applications requiring cutting of material into complex shapes, cutting with increased precision and in small or frequently changing series are ideal for the use of cutting lasers. Drilling lasers are used wherever small diameter holes need to be drilled. A wide range of materials such as metals, plastics, natural and other materials can be cut and drilled.
Welding
Laser welding has a number of advantages that cannot be achieved by any other technique. Since the action of the laser is only local, there is no thermal damage around the weld and thus the entire product. The weld itself is non-porous and does not contain foreign matter. Thanks to high peak energy values, it is also possible to weld materials with a high melting point as well as highly reflective materials (Al, Au). The laser makes it possible to perform micro-welds and even normally inaccessible places can be welded.